PPVC : Why does it matter in Singapore Properties
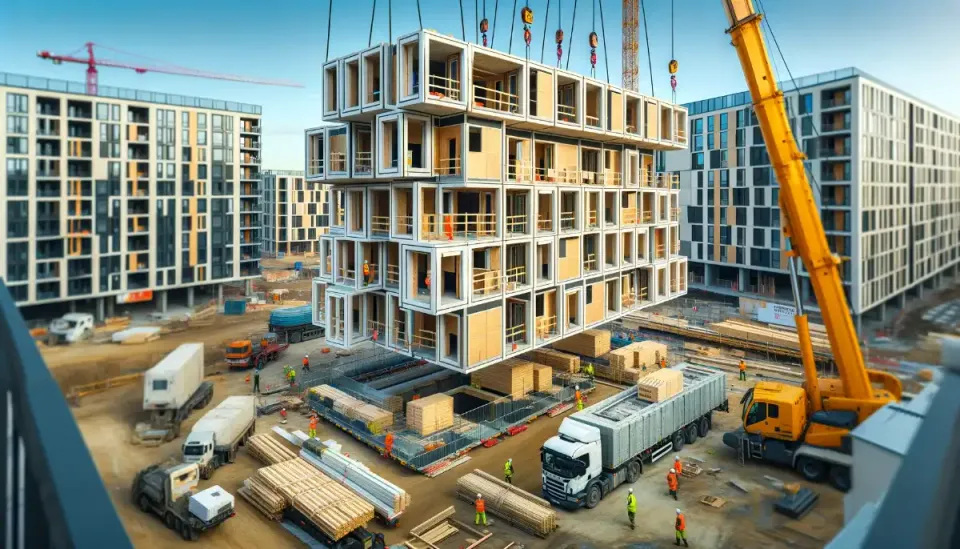
In the previous article, we talked about how Lentoria is selling itself as a "non-PPVC" development, besides the fact it is within 1 km to CHIJ St Nicholas Primary School.
What is this "Lego" Building Method in Singapore?
And most importantly, why does it even matter ?
The Current State of PPVC in Singapore
In Singapore, HDB is one of the major developers using the PPVC construction method. New HDBs are increasingly using prefabricated PPVC modules where possible. According to HDB, as many as 70% of entire structural concrete used during the construction stage is from these prefabricated modules.
In the private properties, more and more developers are using PPVC to build their new launches. In fact, reaching a height of 192 metres for the 56-storey twin towers, Avenue South Residence is the world's tallest PPVC residential building when completed in the first half of 2023, surpassing UOL's own record for the 40-storey The Clement Canopy, which was completed in 2019.
What is PPVC or Prefabricated Prefinished Volumetric Construction
Prefabricated Prefinished Volumetric Construction (PPVC) is a construction method whereby free-standing 3-dimensional PPVC modules are completed with internal finishes, fixtures and fittings in an off-site fabrication facility, before it is delivered and installed on-site at the location where the real estate apartment is.
It is an advanced construction method in Singapore that significantly streamlines the building process for apartments and other structures. BCA has a great section in their web site on this technology.
While PPVC is suitable for many types of construction, its effectiveness and efficiency are particularly notable in high-density residential projects, like apartment buildings, where repetitive layouts are common.
PPVC makes use of Modular Construction Technique which involves constructing large-scale modular units off-site. These units include walls, floors, ceilings, and sometimes even pre-installed furnishings and fittings. Each module is a substantial part of a building, like an entire room or a section of a room.
Advantages of PPVC
- Speed : You can immediately imagine that one of the biggest advantages of PPVC is the considerable reduction in construction time. Since modules are built off-site in a controlled environment, the construction process is less affected by weather and other external factors. This leads to a faster overall building timeline.
- Quality : Building in a controlled factory setting allows for better quality control. The construction conditions are optimal, and there's a consistent level of craftsmanship, which often results in higher-quality finishes.
- Environmental Impact: PPVC is generally more environmentally friendly compared to traditional construction methods. It typically produces less waste and reduces on-site noise and dust. This is particularly beneficial in urban settings or sensitive environments.
- Safety: Because some of the work are done in factories, so the safety of the workers are much higher compared to building the apartment on site.
- Cost Implications: While the initial cost of PPVC can be higher due to the technology and processes involved, it can potentially lead to cost savings in the long run. Savings come from reduced labor costs, faster construction times, and less waste.
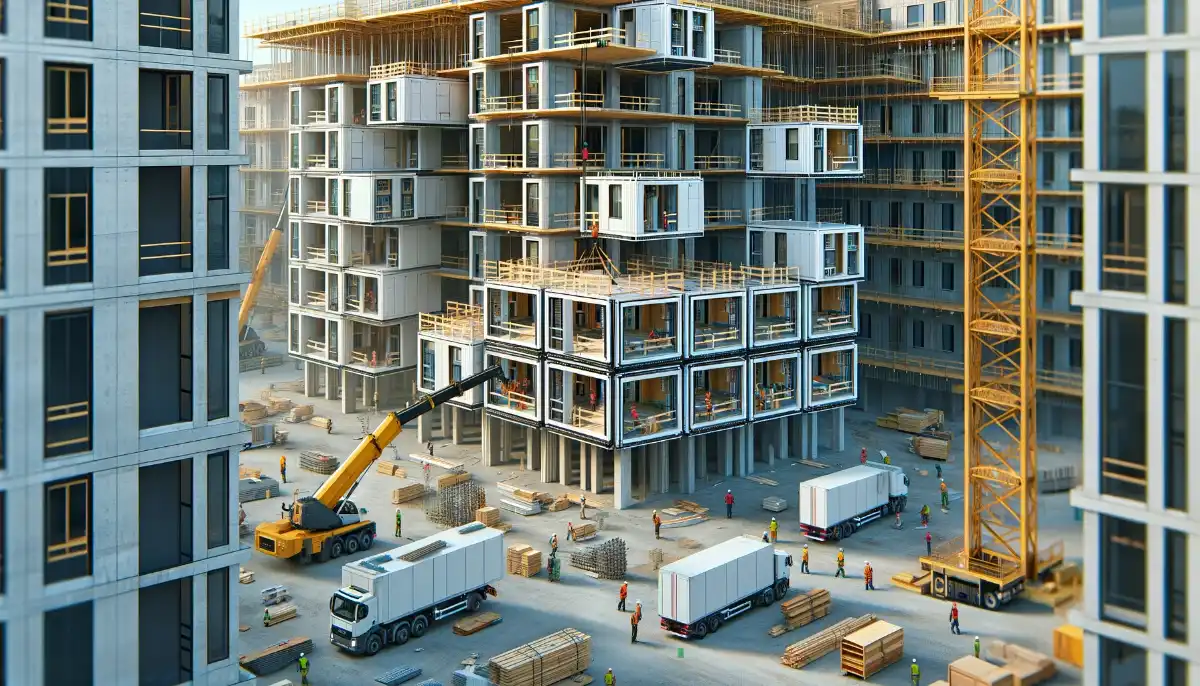
Disadvantages of PPVC
While Prefabricated Prefinished Volumetric Construction (PPVC) offers many advantages, there are certain reasons why some people may not prefer apartments built using this method:
- Logistics and Assembly: Once the modules are constructed off-site, they are transported to the building site. Here, they are assembled and stacked, much like building blocks, to form the complete structure. This requires precise engineering and planning, as the modules need to align perfectly.
- Perceived Lack of Uniqueness: PPVC involves the use of standardized modules, which can lead to a perception that buildings lack uniqueness or character. People who value highly customized or architecturally distinct homes might see PPVC apartments as too uniform or cookie-cutter.
- Design Limitations: Although PPVC technology has advanced, there can still be limitations in design flexibility compared to traditional construction methods. This might affect the variety of layouts, ceiling heights, and the ability to make structural changes or renovations in the future.
- Transportation and Size Constraints: The size of PPVC modules is often limited by transportation logistics (such as road width and height restrictions). This can restrict the size of rooms or lead to design compromises that wouldn't be necessary with traditional construction methods. In fact, ceiling heights of PPVC apartments are
Interesting Point : It is a rule to use PPVC for Toilets
Prefabricated Bathroom Unit (PBU) is a bathroom unit, which is preassembled off-site complete with finishes, sanitary wares, concealed pipes, conduits, ceiling and bathroom cabinets, before it is delivered and installed on-site.
The use of PBU is required for all residential non-landed and residential non-landed components of mixed-use developments on Government Land Sale (GLS) sites from 1 November 2014 onwards.
Like this picture 😀
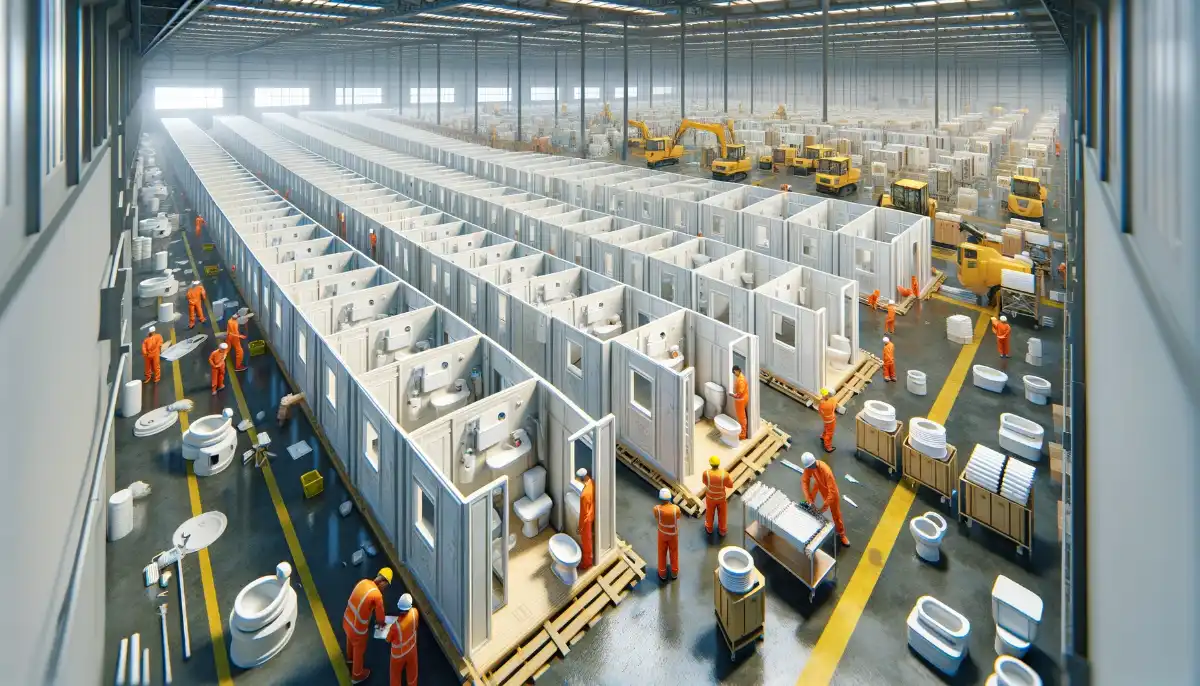
So why does it matter in the end ?
Two main reasons for buyers who want to know if their development is a PPVC built (or not, as in Lentoria's case).
Ceiling Height and Room Width of the Units
PPVC units generally feature ceiling heights of 2.75 meters and room widths of 2.8 meters. On the other hand, conventionally constructed condominiums often provide higher ceilings, ranging from 2.9 to 3.3 meters, and they don't have restrictions on room widths.
The reason behind these size limitations in PPVC units is linked to transport constraints. According to traffic regulations, transport trucks must not exceed a height of 4.5 meters to travel on public roads without needing police escorts. The achievable ceiling height in a PPVC unit is determined by deducting the height of the truck's platform and the thickness of the module's floor or ceiling slab.
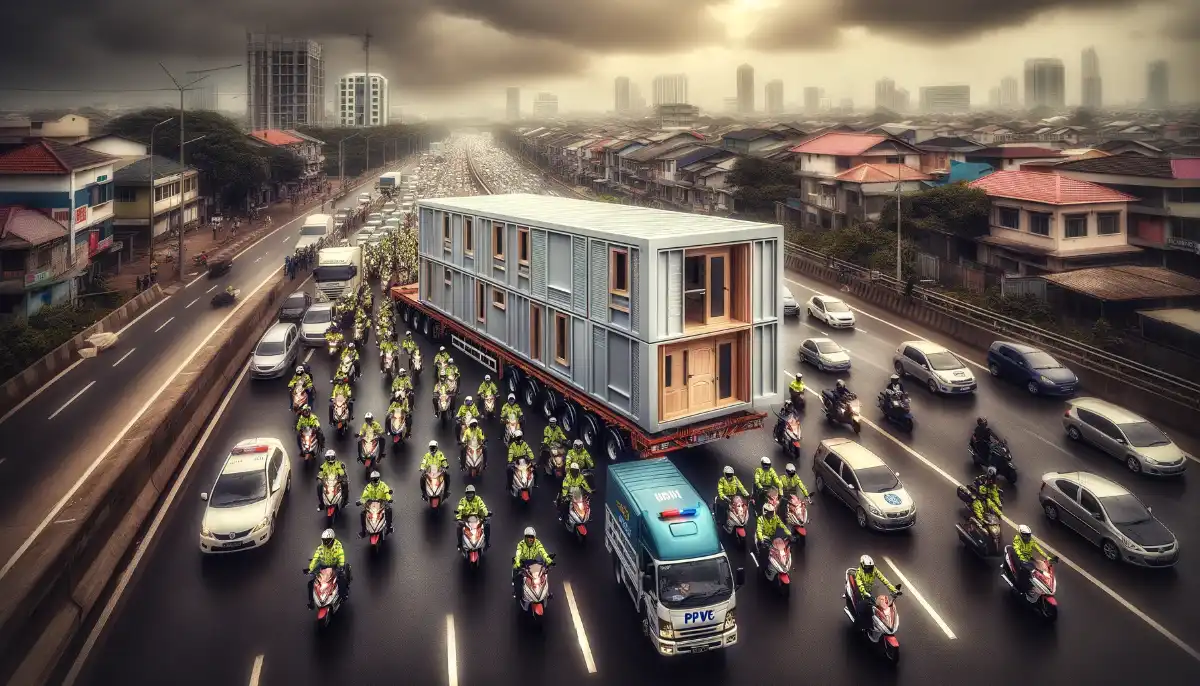
Regarding the room width in PPVC units, it is constrained by the maximum allowed vehicle width of 3 meters on roads, minus the thickness of the walls.
As a result, the term "Cookie Cutter" has been unfairly used on PPVC condos as they "looked the same, feel the same, and maybe are made in the same factory" 😸
Hacking of Walls or other common renovation works
"Hacking" walls are harder in apartments made with Prefabricated Prefinished Volumetric Construction (PPVC) compared to normal buildings. In PPVC, each section is built to support itself, and the walls are very important for keeping the whole part stable. Changing these walls can cause problems for the structure of the section and maybe even the whole building.
Also, PPVC sections usually have important things like plumbing, electrical wires, and heating/cooling systems built into the walls. If you hack into a wall, you might break these systems. This can lead to more problems and you might need to do a lot of fixing or repairs to the built in stuff. This makes hacking walls in PPVC buildings more complicated than in regular buildings.
As such, in many PPVC projects, the walls are not hackable; so you may not have the option of, say, knocking down a wall to join up two smaller bedrooms.
Conclusion
So does it matter to you ? Will the idea that a condo is "non PPVC" matters to you as a buyer or not ? Share your views in the comments !
Member discussion